GCS can custom make conveyor rollers
GCS can manufacture rollers to your specifications, applying our years of experience in materials and design for both OEM and MRO applications. We can provide you with a solution to your unique application.
Custom options include but many times not limited to:
Component materials:
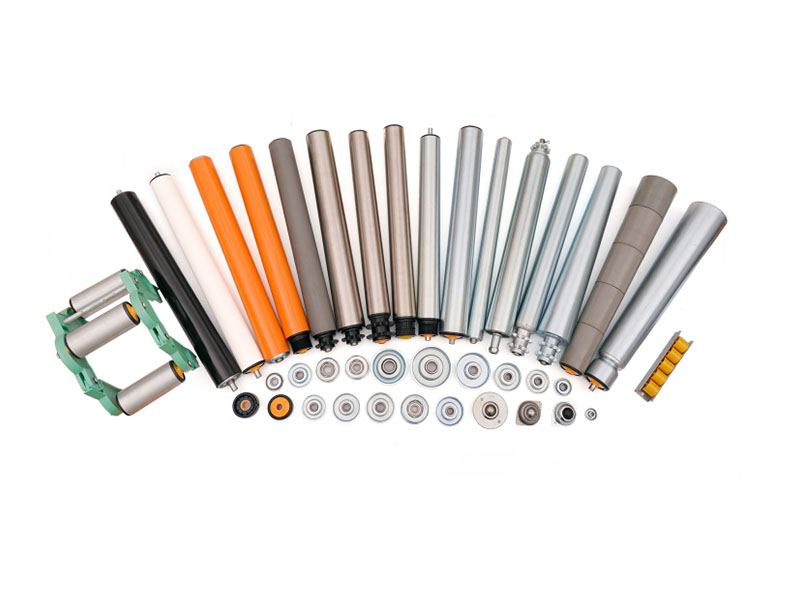
GCS Conveyor Rollers
We manufacture a wide selection of conveyor rollers with options to meet most of your material handling needs. If you cannot find a standard roller to fit your application, we can likely produce a custom conveyor roller to meet your needs. For conveyor rollers, it is important to make sure you provide the proper measurements to ensure the roller will fit properly. We can help you find the right roller for your application by using your conveyor system’s measurements.
Non-Powered Rollers in Gravity Conveyor Rollers are the most popular and simple method of conveying goods. The rollers are not powered. Goods are moved and conveyed by gravity or by human power. Conveyors are usually arranged horizontally or inclined.
Gravity roller is a device widely used in light material conveying systems. It uses the object's own gravity to promote the movement of the object. Typically, gravity rollers are made of metal, plastic, or composite materials and have a flat outer surface. They come in two common designs: straight rollers and curved rollers.
To accommodate different load sizes and weights, adjustable conveyor rollers can be integrated into gravity conveyor systems for enhanced versatility.
These belt rollers design the appearance and configuration of the rollers to suit different conveyor belts. A belt driven roller conveyor system is a series of structurally supported rollers that are driven by a belt.
The appearance and configuration of the rollers are designed to suit different conveyor belts.
These sprocketed heavy-duty conveyor rollers are used to replace or upgrade the rollers on heavy-duty chain-drive conveyors. Also known as chain-drive live rollers, they are ideal for moving heavy items such as pallets, drums, and bulk containers. The sprocketed rollers have teeth that engage with the drive chain to prevent the chain from slipping, even in dirty or oily conditions. These conveyor rollers are installed in roller conveyors to support and move items on the conveyor. The rollers let loads roll from one place to another, reducing the effort it takes to move the loads.
Conical rollers are also called curved rollers or conus rollers. These conveyor rollers are predominantly employed in piece goods conveyor systems to These conveyor rollers are predominantly employed in piece goods conveyor systems to allow for realizing curves or junctions.
Conical rollers typically have a tapered shape, with a larger diameter at one end and a smaller diameter at the other end.
This design allows the rollers to smoothly guide materials around curves in a conveyor system.
Conveyor Rollers Replacement That’s Customized to Your Requirements
In addition to a large number of standard sized rollers, we are also able to craft individual roller solutions for niche applications. If you have a challenging system that needs rollers that are made to your particular dimensions or that need to be able to cope with a particularly tough environment, we can normally come up with a suitable answer. Our company will always work with customers to find an option that not only delivers the required objectives, but which is also cost-effective and able to be implemented with minimal disruption. We provide rollers to a wide range of industries, including companies involved in ship building, chemical processing, food & beverage production, transport of hazardous or corrosive substances and many more.
Some Custom Conveyor Roller Design Options Include:
Because custom rollers are not returnable, we require that you call and talk to one of our application specialists to make sure you get the proper solution to your unique application.

Hog Ring holes in the axle.

Threaded ends on the axle.

Drilled and tapped axle ends.

Multiple Grooves, custom groove locations.

Sprocket, custom sprocket locations.

Crowned rollers.And more!
Versatile, Customized Conveyor Systems that Last
GCS present the most versatile conveyor system rollers to suit any application. Constructed using the highest quality roller conveyor system workmanship and designed to stand even the most rigorous use, our rollers provide function and utility that you can trust.
A Wide Range of Materials
Is corrosion an issue with your processing or manufacturing business? You should consider our plastic roller or one of our other non-corrosive options. If so, consider our pvc conveyor rollers, plastic conveyor rollers, nylon conveyor rollers, or stainless conveyor rollers.
We have the custom heavy duty roller conveyor system that you need. Conveyor Systems conveyor roller manufacturers can give you heavy duty conveyor rollers, steel conveyor rollers and durable industrial rollers.
Increased Workflow Capacity
A busy warehouse facility requires robust solutions for maximum productivity. While labor costs and shipping times may be blowing out your budget, installing our high quality conveyor roller can dramatically increase your workflow capacity. By speeding up the processes that you use to deliver your goods by using high quality conveyor system rollers, you will see benefits in many aspects of your facility. From a reduced burden on your employees to meet demands, as well as a safer and more efficient workplace environment, you will see a higher level of customer satisfaction and most importantly, an increase in your bottom line.
Improved Safety Measures for Any Warehouse or Facility
GCS is committed to providing the most safe and reliable rollers to suit any system or process in a busy working facility, whether the conveyor uses a gravity or powered mechanism of action. A strong and long lasting effect is produced through self-lubrication offered on many of our rollers. Suitable for a range of applications including food handling, chemical transport, volatile material movement and high capacity warehousing, our range of custom conveyor system rollers are backed by our service guarantee that ensures safe and efficient use in a consistent and durable manner.
Cost Effective Approach to Time Management
Implementing a robust conveyor roller solution to your facility need not be the expensive effort that it once was. GCS offers the most extensive range of custom conveyor rollers designed to reduce your overheads while saving you time. By automating your in-facility transportation processes with stronger and loner lasting rollers, the initial investment on implementing your conveyor roller will save you money on labor costs. With a focus on durability and use within a wide range of applications, our rollers far outperform more expensive products.
Contact GCS Today to Learn More
Finding the perfect roller for your operation is crucial, and you want to do so with little disruption to your workflow. If you need a special-size roller for your conveyor system or have questions about the rollers’ differences, we can assist you. Our customer service team can help you get the right part for your existing conveyor system.
Whether installing a new system or needing a single replacement part, finding suitable rollers can improve your workflow and increase your system’s life. We will help you get the right part with fast communication and personalized care. To learn more about our rollers and custom solutions, contact us online to speak with a specialist or request a quote for your roller needs.
Frequently asked questions about conveyors roller
A conveyor roller is a line in which multiple rollers are installed for the purpose of transporting goods in a factory, etc., and the rollers rotate to transport the goods. They are also called roller conveyors.
They are available for light to heavy loads and can be selected according to the weight of the cargo to be transported.
In most cases, a conveyor roller is a high performance conveyor that is required to be impact and chemical resistant, as well as being able to transport items smoothly and quietly.
Inclining the conveyor allows the conveyed material to run on its own without external drive of the rollers.
Your rollers must fit your system exactly for optimal performance. Some different aspects of each roller include:
Size: Your products and conveyor system size correlate to the roller size. The standard diameter is between 7/8″ to 2-1/2″, and we have custom options available.
Material: We have several options for roller materials, including galvanized steel, raw steel, stainless steel and PVC. We can also add urethane sleeving and lagging.
Bearing: Many bearing options are available, including ABEC precision bearings, Semi-precision bearings and Non-precision bearings, among other options.
Strength: Each of our rollers has a designated load weight specified in the product description. Rolcon provides both lightweight and heavy-duty rollers to match your load sizes.
Conveyor rollers are used as conveyor lines to move loads from one location to another, for example, in a factory.
The conveyor rollers are suitable for conveying objects with relatively flat bottoms, as there may be gaps between the rollers.
Specific materials conveyed include food, newspapers, magazines, small packages, and many others.
The roller does not require power and can be pushed by hand or propelled by itself on an incline.
Conveyor rollers are often used in situations where cost reduction is desired.
A conveyor is defined as a machine that continuously transports a load. There are eight major types, of which belt conveyors and roller conveyors are the most representative.
The difference between belt conveyors and roller conveyors is the shape (material) of the line conveying the cargo.
In the former, a single belt rotates and is transported on it, while in the case of a roller conveyor, multiple rollers rotate.
The type of rollers is selected according to the weight of the cargo to be conveyed. For light loads, the roller dimensions range from 20 mm to 40 mm, and for heavy loads up to about 80 mm to 90 mm.
Comparing them in terms of conveying force, belt conveyors are more efficient because the belt makes surface contact with the material to be conveyed, and the force is greater.
Roller conveyors, on the other hand, have a smaller contact area with the rollers, resulting in a smaller conveying force.
This makes it possible to convey by hand or at an incline, and it has the advantage of not requiring a large power supply unit, etc., and can be introduced at a low cost.
A typical 1 3/8” diameter roller has a capacity of 120 lbs. per roller. A 1.9” diameter roller will have an approximate capacity of 250 lbs. per roller. With rollers set on 3” roller centers, there are 4 rollers per foot, so the 1 3/8” rollers would typically carry 480 lbs. per foot. The 1.9” roller is a heavy duty roller that handles approximately 1,040 lbs. per foot. The capacity rating can also vary based on how the section is supported.