Chain Driven Conveyor Rollers
With the growing demand for automation, GCS increasingly relies on automated transportation solutions. Among them, sprocket roller conveyors are the most popular, especially for handling heavy workpieces. These chain driven conveyor rollers offer enhanced safety and reliability, making them a preferred choice across industries.
Regardless of your industry, we can provide tailored conveyor solutions. To ensure stable movement, a smaller roller center distance is recommended. Typically, the workpiece should contact at least three rollers at all times. For heavier loads, larger and thicker rollers are required. Additionally, the roller height relative to the main beam must be considered when using driven sprocket rollers.
Boost Productivity with Sprocket Rollers
Chain Driven Conveyor Rollers are powered by a chain and sprocket system. It provides efficient power transmission, making it suitable for conveyor systems handling heavy materials and offering high load capacity, smooth operation, and customizable options to meet various industrial needs.
Customization Services: Tailor-Made for Your Needs
We recognize that every business has unique requirements. GCS offers comprehensive customization services:
● Size Customization
● Material Selection
● Sprocket Specifications
● Surface Treatment Options
● Special Features
Top 4 Hottest Chian Driven Conveyor Rollers
We offer a number of differently sized chain driven roller options, as well as having the capacity to create custom sprocket rollers. With 30 years of production behind us, we are proud of our reputation for reliable, high-quality products and excellent customer care at every stage of your dealings with us.
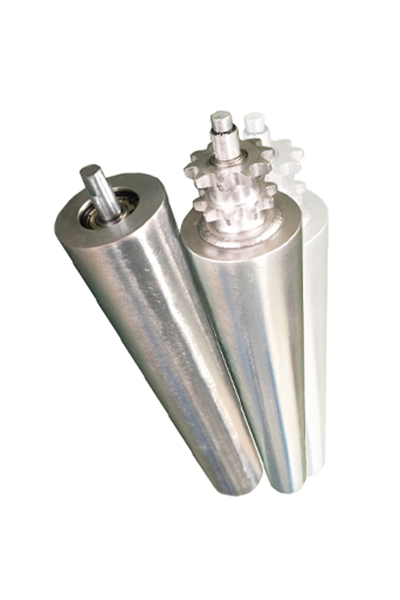
Sprocket rollers with Welded steel tooth
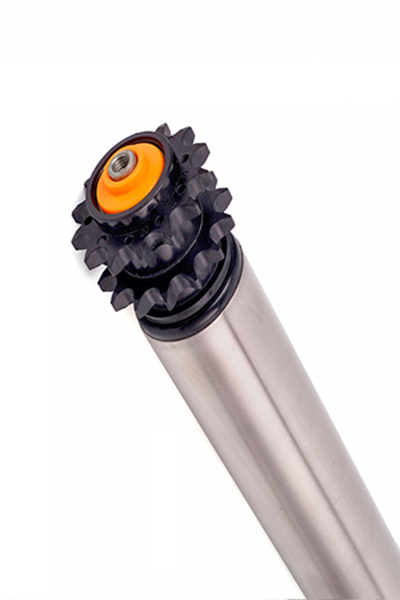
Sprocket rollers with Plastic tooth
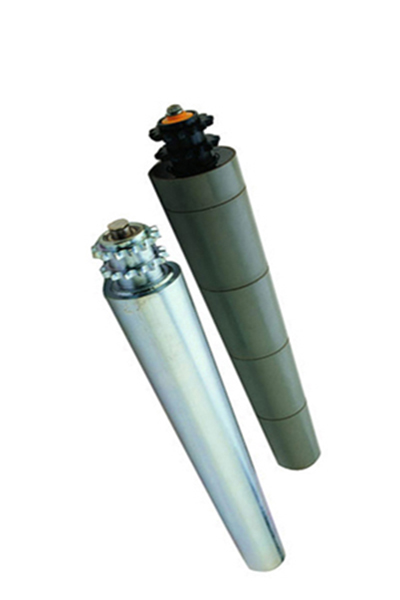
Sprocket rollers with Steel Tooth
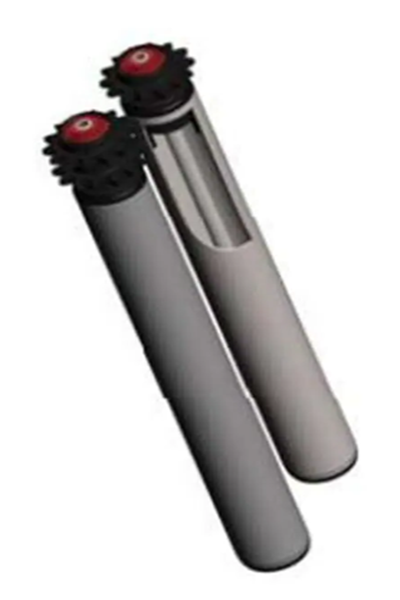
Sprocket rollers nylon tooth
Key Specifications
Tube | Shaft Size | Bearing |
30mm diameter x 1.5mm | 6mm ,8mm, 10mm diameter | Semi-precision steel swaged |
1 1/2" diameter x 16 swg | 8mm, 10mm, 7/16"*, 12mm diameter & 11 hex | Semi precision steel swaged |
1 1/2" diameter x 16 swg | 12mm, 14mm diameter & 11 hex | Precision plastic push-in complete with 60022RS and blue plastic insert |
1 1/2" diameter x 16 swg | 8mm, 10mm, 7/16", 12mm diameter & 11 hex | Precision steel swaged |
50mm diameter x 1.5mm | 8mm, 10mm, 7/16", 12mm diameter, & 11 hex | Semi precision steel swaged |
50mm diameter x 1.5mm | 8mm, 10mm, 7/16", 12mm diameter, & 11 hex | Precision steel swaged |
50mm diameter x 1.5mm | 12mm, 14mm diameter & 11 hex | Precision plastic swaged complete with 60022RS & blue plastic insert |
Roller Mounting Options Available
Gravity Or Idler Rollers Coating Options
Zinc Plating
Zinc plating, also known as Zinc Blue white passivation, is a widely used coating process for rollers. It provides a shiny white appearance with a thickness of 3-5 microns. This process is cost-effective and faster compared to other coating methods. To enhance performance, adjustable conveyor rollers can be finished with various coating options tailored to specific applications.
Chrome Plating
Chrome plating is a rarely used process, typically employed when rollers are at risk of scratches, as it provides excellent protection. It is a very costly and time-consuming process compared to other plating methods. Auto-ancillary companies prefer chrome plating when conveying metal parts due to its superior durability and corrosion resistance.
PU Coated
PU coated rollers utilize polyurethane coating, typically applied when metal conveying parts require protection from scratches or metal-to-metal friction. A 3-5 mm thickness layer is generally applied to the roller, though this can be increased as needed. Most GCS customers prefer this process for conveying metal parts due to its durability and smooth, bright, shiny finish available in various colors like green, yellow, and red.
PVC Sleeve
PVC sleeve coated rollers feature a 2-2.5mm thick PVC sleeve that is carefully inserted onto the roller under high pressure. This process is used when enhanced friction or grip on the rollers is required, making it ideal for applications where materials need to be securely conveyed. It also provides reliable performance and durability, ensuring smooth and efficient operation in various industrial settings.
Benefits of Chain Driven Conveyor Rollers
✅ High Load Capacity: Engineered for heavy-duty applications, ensuring system stability.
✅ Low Noise Operation: Optimized chain engagement and high-quality bearings reduce noise for a quieter workplace.
✅ Long Service Life: Rigorously selected materials and precision manufacturing result in superior longevity.
✅ Easy Maintenance: Modular design allows for easy disassembly and replacement, reducing downtime.
✅ Versatile Applications: Suitable for industries such as food, chemical, logistics, and manufacturing, meeting diverse operational needs.
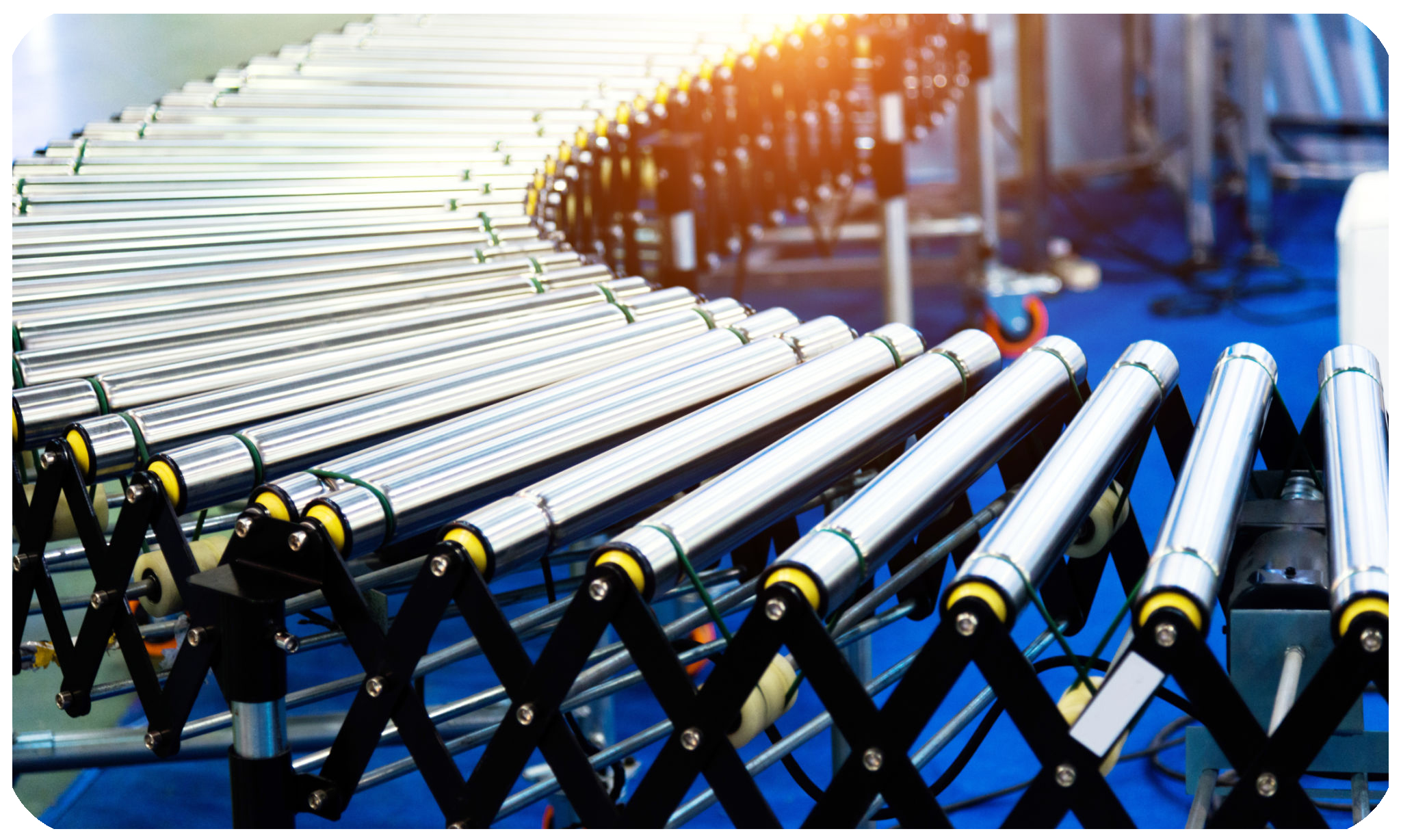
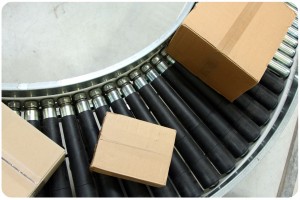
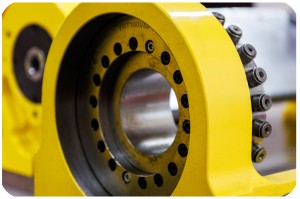
Optimize Your Conveyor System
Partner with Global Conveyor System Supplier Company Limited in China for reliable, efficient chain driven conveyor rollers tailored to your operational needs.
Chain Driven Conveyor Rollers
When it comes to chain-driven conveyor rollers, experience makes all the difference. With over 30 years in the material handling industry, GCS brings the expertise you need. Our team takes a consultative approach, working closely with you to understand your specific requirements. We keep you involved at every step, ensuring accurate and on-time delivery. GCS offers both industry-standard and custom-engineered conveyor rollers, available in various configurations and installation styles to suit a wide range of applications. Whether you're handling food, chemicals, volatile materials, bulk goods, or raw materials—whether you need powered or gravity-aided conveyors, high-speed, or variable-speed systems—we have the right solution for you.
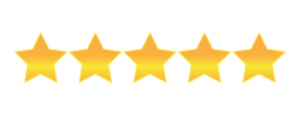